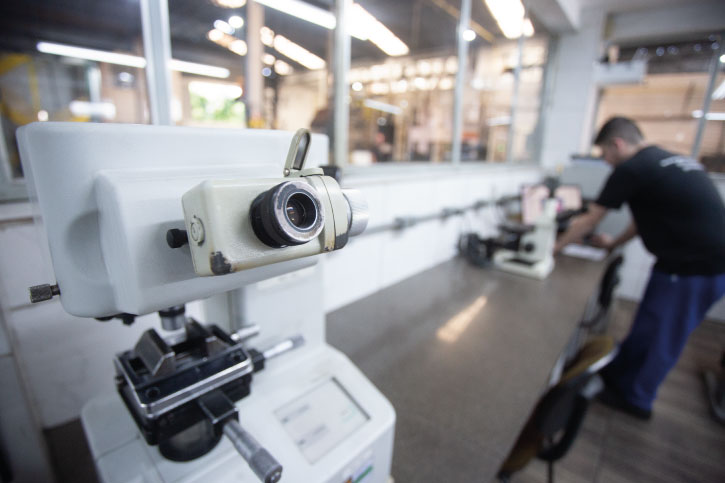
Leandro José de Almeida , Fernando Suzumura Kawata, Rafael Neves de Almeida, Lucelio Siqueira – Meritor. O processo de Fabricação do parafuso tem como fluxo após vergalhão trefilado na usina, a conformação mecânica em dois estágios, sendo cabeça e corpo, assim como a região da rosca sendo conformada por usinagem, o processo num todo também consistena utilização do fosfato de manganês para auxiliar no processo de conformação, desde o processo de trefilação dos vergalhões na Usina até o processo de conformação final dos parafusos. Para que os parafusos consigam atingir a resistência necessária para suportar carregamentos de torção, impacto e tração se faz necessário o tratamento térmico de Tempera e Revenimento. Antes do parafuso entrar no forno de Tratamento Térmico é extremamente importante que ocorra a desfosfatização, para garantir que o Fósforo residual presente na superfície do parafuso não difunda para o interior da peça e forme uma fase rica em Fósforo, com baixa resistência denominada Ferrita Delta. Com esse trabalho poderemos concluir se realmente a fase Ferrita Delta reduz a vida em fadiga com análise da Curva S-N e reduz também a resistência ao torque. A fase Ferrita Delta não somente é caracterizada pela análise microscópica, como também no MEV via EDS com a comprovação do elemento Fósforo, com isso vamos expor o parafuso a concentrações diferentes de fosfato de manganês em um mesmo tempo de forno na tempera e também com tempos de forno nsa temperas distintos em uma mesma concentração de fosfato de manganês. Assim vamos entender qual a variável que mais difunde a Ferrita Delta e após essa constatação, estudar não somente a fragilização devido a fase Ferrita Delta, mais também a relação de percentual/profundidade de Difusão de Ferrita Delta X resistência ao Torque.
Sabemos que uma falha de componentes em veículos pode originar um risco potencial ao condutor sofrer um acidente, para o próprio condutor ou terceiros. Parafusos para tal aplicação requer alta resistência quando utilizados em diferenciais de caminhões, e sofrem altas solicitações mecânicas, que se faz necessário processos de fabricação especialmente para obtenção de propriedades para que possam suportar esses esforços, aumentando sua resistência ao torque e a fadiga. Históricos de falha de campo e linha mostram que o problema que tais parafusos apresentavam uma camada branca na superfície, camada com grande dureza e fragilidade. Analisando essa camada se concluiu que ela surgiu em função da presença residual de fósforo proveniente do processo de fosfatização de manganês, difundindo no aço durante o tratamento térmico de tempera. A fosfatização de manganês é necessário, pois serve de ancoradouro agindo como um lubrificantes e outros redutores de atrito, facilitando assim, o processo de conformação mecânica a frio de trefilação entre outros. Se expormos o parafuso no fosfato de manganês, haverá a formação da fase frágil conforme Cioto et al. (2008), responsável pela falha prematura do parafuso quando observada em campo ou em processo de linha de montagem. Com o já dito, objetivo deste Artigo é mostrar o efeito prejudicial da Ferrita Delta quando em solicitação mecânica, mostrando sua influência quando relacionado ao limite de resistência ao Torque em função do percentual e/ou volume de Ferrita Delta.
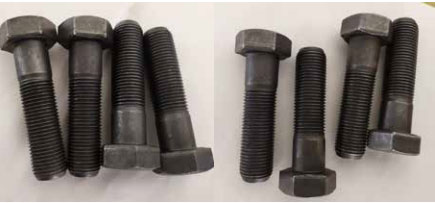
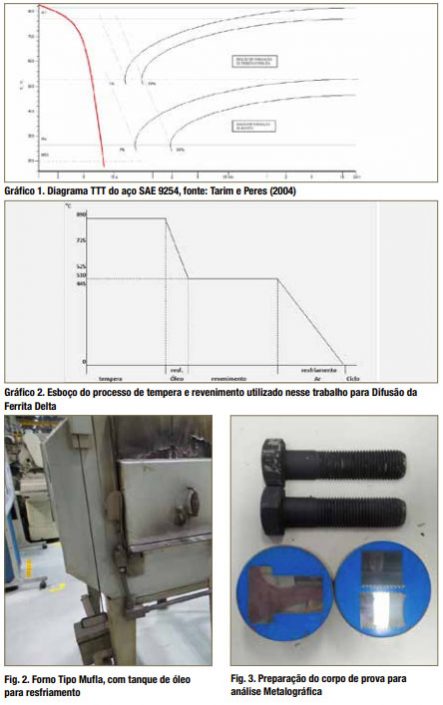
Referência Bibliográfica Durante o processo de conformação mecânica algumas variáveis são de extrema importância, podemos considerar o Ishikawa para entender essas variáveis, algumas estão ligadas ao processo, como lubrificação, assim como também àqueles relacionados ao material como à qualidade da matéria prima, por exemplo, microestrutura do aço a ser conformado, propriedades mecânicas, etc. Se o material não estiver adequado a aplicação, isso pode levar a problemas como nucleação e propagação de trincas, redução de vida útil e fragilização no parafuso. Os processos de trefilação de vergalhões, extrusão a frio, forjamento a frio, etc. Estas operações que envolvem deformação a frio, em uma condição em que a transferência de calor e massa seja baixa, faz com que estas operações requerem uma boa lubrificação da superfície a ser deformada, sendo possível através da aplicação do fosfato na usina seguido da adição de sabão em processos de extrusão e trefilação. Sabões de trefila são reativos de estearatos alcalinos transformam a camada de fosfato de zinco em um estearato de zinco de alto poder lubrificante que adere à superfície. O fluxo de conformação mecânica consiste de forjamento a frio e laminação de rosca, o parafuso estudado é de classe de dureza superiores a 22HRC e portanto, necessitam de serem submetidos ao tratamento térmico de têmpera resfriada em óleo e revenimento ao ar, porém, quando exposto ao fosfato e se obtiver resíduos de fosfato, o material após tempera acarretará a formação da fase delta (ferrita delta, Fe3P ou fosfeto de ferro), como mostrado na figura X, caracterizada como uma camada branca. Em temperatura próxima de 723°C e durante a austenitização, o fósforo residual presente na peça conformada pode difundir para o interior do metal, formando essa fase frágil rica em fósforo. Em processos de fabricação de parafusos, para evitar a formação da camada branca é recomendada a remoção do fosfato com um tratamento de desfosfatização (desengraxante alcalino) antes do tratamento térmico de têmpera, principalmente em atmosferas descontroladas. A fase estudada rica em fósforo difundida na superfície dos parafusos, apresenta alta dureza, por volta 45 HRC, com profundidades variadas, quanto mais resíduo maior a difusão e uniformidade da camada, reduzindo assim a resistência ao torque e a fadiga. Materiais e Métodos Inicialmente utilizamos parafusos classe 12.9 na liga SAE 4140, onde fizemos a exposição dos mesmos em banho de fosfato em diferentes concentrações. Tratamento Térmico A tempera do material foi realizada com resfriamento em óleo para analisar microscopicamente a relação do tempo de exposição do fosfato X percentual e/ou profundidade de difusão da Ferrita Delta. Temperamos as peças conforme Diagrama abaixo, porém, dentro do faixa de transformação de Ferrita Delta.
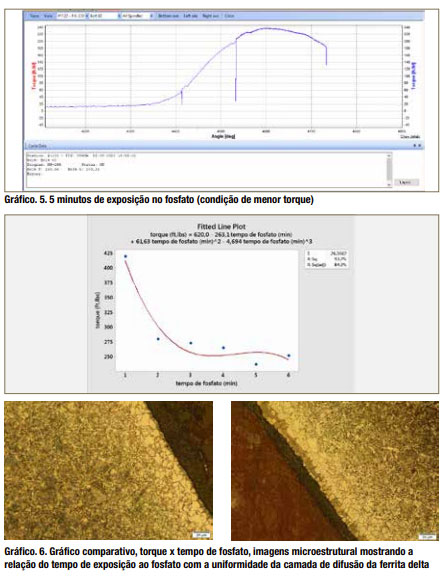
Para o processo de Tempera e Revenimento, utilizamos um forno tipo Mufla. Análises Microscópicas das Amostras de 1 a 6 minutos de Exposição em Banho de Fosfato de Manganês Para as análises metalográficas, fizemos a preparação do corpo de prova com corte em cut of, seccionando o parafuso longitudinalmente, embutimento com termofixo baquelite em embutidora, desbaste em lixa #120, #400, #600, polimento em politriz com pasta de diamante e ataque químico com nital 2 a 5%. Para caracterização da microestrutura, utilizamos um microscópio ótico Olympus, com objetiva de 50X e ocular 10X (500X). Observado presença de Ferrita Delta uniforme e dispersa na Superfície do material, ataque nital 2%, estrutura Martensítica, aumento 500X (Fig. 4). Observado presença de Ferrita Delta dispersa, porém de forma mais uniforme na Superfície do material, ataque nital 2%, estrutura Martensítica, aumento 500X (Fig. 5). Observado presença de Ferrita Delta dispersa, porém de forma mais uniforme na Superfície do material, ataque nital 2%, estrutura Martensítica, aumento 500X (Fig. 6). Observado presença de Ferrita Delta dispersa, porém de forma mais uniforme na Superfície do material, ataque nital 2%, estrutura Martensítica, aumento 500X (Fig. 7) Observado presença de Ferrita Delta dispersa, porém de forma mais uniforme na Superfície do material, ataque nital 2%, estrutura Martensítica, aumento 500X (Fig. 8). Dureza encontrada nos testes, conforme Curva de Gauss (Gráfico 3, 4, 5, 6 e Fig. 9) Teste Mecânico Após expor os parafusos em tempos diferentes de fosfato de 1 a 6 minutos e tratar termicamente para a difusão da Ferrita Delta, testamos o torque.
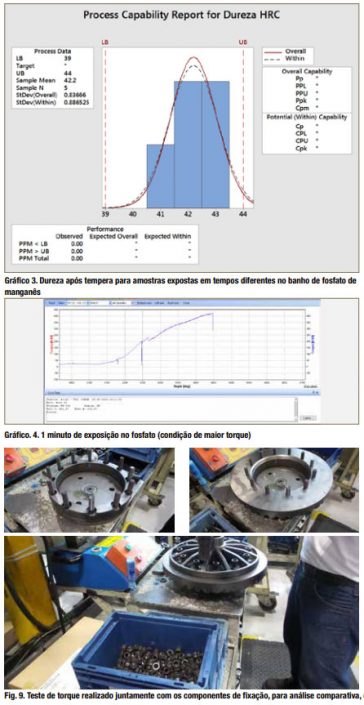
Analisamos no MEV a camada de Ferrita Delta para comprovação da difusão do fosforo, mostrando que se trata realmente da Ferrita Delta e não de uma descarbonetação. Conclusão Os teste iniciais mostraram que existe uma redução de resistência ao torque quando exposto a tempos de fosfato maiores, ou seja, quanto mais uniforme a camada difundida a resistência ao torque tende a cair. A resistência quando comparado entre 1 e 5 minutos caiu 56%, mudando também a curva de escoamento. Observamos também que existe um limite máximo de difusão do fosfato, acima de 5 minutos provavelmente a difusão se mantenha e a tendência seja a mesma na relação ao torque, se tornando um ponto de saturação da Ferrita Delta difundida no parafuso.
Futuros: Para trabalhos futuros sugerimos fazer um comparativo, porém, indo mais a fundos nas propriedades mecânicas, avaliando também, o limite de resistência a tração e a vida em fadiga.
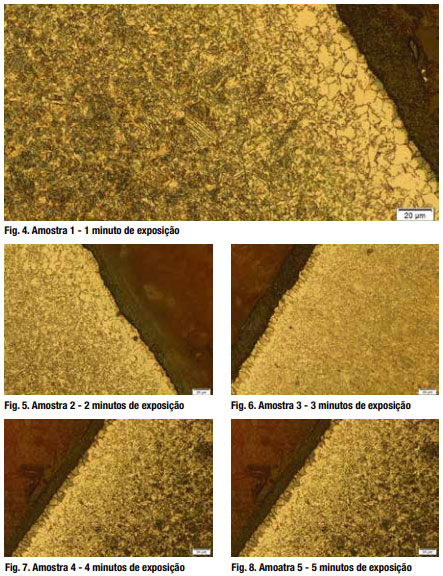
Referências [1] CALLISTER, W.D. Materials science and engineering an introduction. 7thed. New York: John Wiley, 2007. p.290-300. [2] CIOTO, R.; COLLARES, A.R.; ZUFFO, C.H. The Effect of delta ferrita on the fatigue behavior of high resistance threaded fastener. Warrendale: SAE, 2008. (Paper SAE 2008-36-0063E). [3] FORSYTH, P.J.E. A Two stage process of fatigue crack growth. In: CRACK PROPAGATION SYMPOSIUM, 1961, Cranfield. Proceedings… Cranfield: Cranfield College of Aeronautics, 1961. v.1, p.76-94. [4] PANOSSIAN, Z. Fosfatização dos metais ferrosos. São Paulo: ABM, 2007. p.50- 80. [5] COLPAERT, H.; COSTA, A.L.S. Metalografia dos produtos siderúrgicos comuns. 4.ed. São Paulo: Edgard Blücher, 2008. p.409-416. [6] SURESH, S. Fatigue of materials. Cambridge: Cambridge University Press,